Rankine cycle
Published on 9 October 2022
A Rankine cycle is a method to convert a source of heat into mechanical energy, which can then optionally be converted into electricity.
When working with a heat source at modest temperature, expanding the gaseous working fluid to recover mechanical power within the turbine leads to partial fluid condensation, i.e. transition of some of the working fluid into the liquid phase. From a technological point of view, pumping that mixture of liquid and gas back to close the cycle is a lot more difficult than pumping either liquid or gas.
A Rankine cycle is purposely built to ensure full transition from the gaseous state to the liquid state before pumping and then full transition from the liquid state to the gaseous state before expansion to avoid such technological difficulties. Even if in theory a Rankine cycle is less efficient than a Carnot cycle, it gives better results in practice because pumping/expanding single phase fluids creates less parasitic losses and therefore an efficiency that is closer to the theoretical cycle efficiency.
Phase diagram
As the Rankine cycle is intrinsically linked to phase diagrams, it is important to correctly understand the basic fluid properties first. Let us consider the water/steam diagram as steam-based Rankine cycles are among the most common applications.
At ambient pressure (~100 kPa) and temperature, water is liquid with a density of ~1000 kg/m3 or a specific volume of 0.001 m3/kg. If heat is provided, temperature increases up to 100 ºC, then some steam appears at a density of only about ~0.58 kg/m3 (a specific volume of ~1.7 m3/kg). In-between the low specific volume in the liquid state and the high specific volume in the gaseous state, there is a region that cannot be reached in single-phase form. In this region, there is an equilibrium between a fraction of liquid (green curve left of the critical point) and a fraction of gas (green curve right of the critical point).
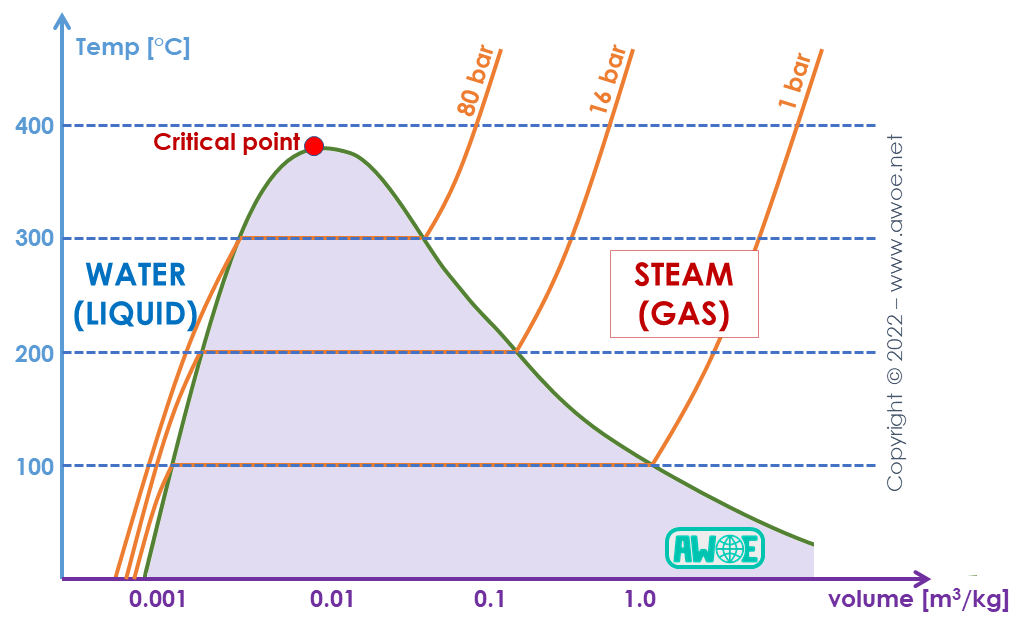
T-v diagram for water/steam
If pressure is further increased, that region of two-phase equilibrium becomes narrower until the critical point is reached. At the critical pressure, liquid could be directly converted into gas and vice versa without any intermediate partial composition in-between. Above this critical pressure, however, there is no distinction anymore between liquid and gas. For water this critical pressure is at about 221 bar and about 647 K (about 374 ºC).
The same information plotted in a Temperature-entropy diagram results in the following figure, with the gaseous phase to the right of the bell shape, the liquid phase to its left and the co-existence region within the bell shape.
Because of the bell shape and the existence of the critical temperature, there is an obvious difference between a low-temperature heat source (below the critical temperature) operating with a subcritical Rankine cycle and a high-temperature heat source (above the critical temperature) potentially operating with a supercritical cycle.
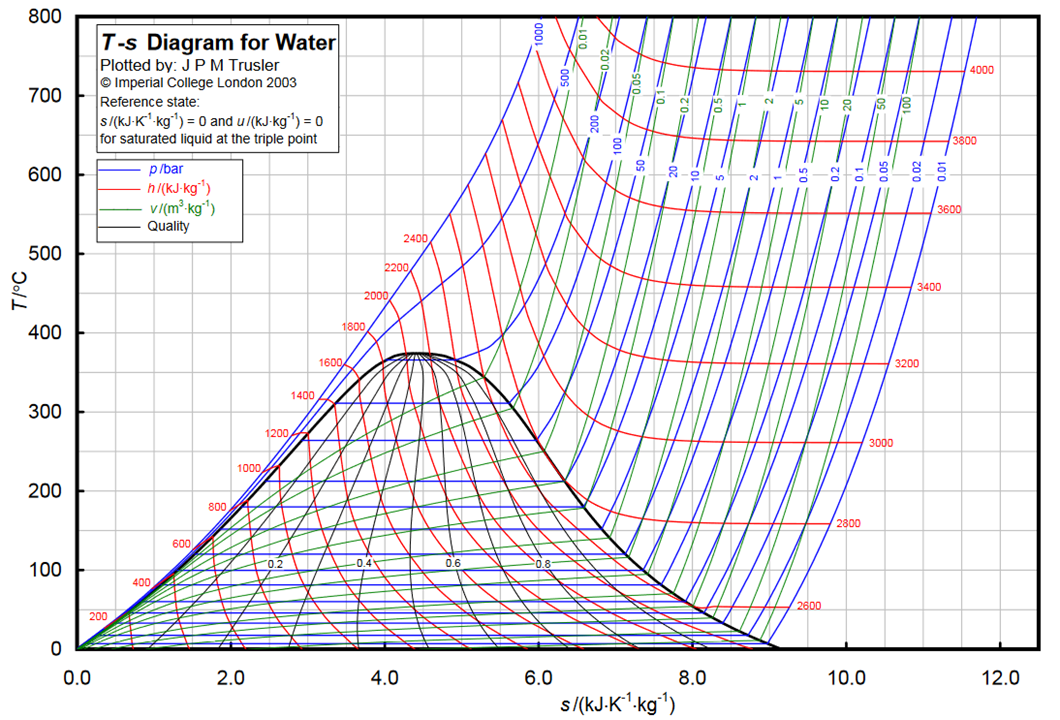
T-s diagram for water/steam
Base subcritical Rankine cycle
With a heat source that cannot heat water/vapour above the critical point, the cycle will operate at a pressure below the critical pressure of 221 bar. As the amount of mechanical energy recovered during expansion in the turbine is linked to the expansion ratio (the ratio of pressures before and after expansion), this effectively restricts the recoverable energy and the global cycle efficiency.
Starting from water at ambient pressure (green dot), a liquid pump increases water pressure up to 100 bar (orange dot) in the example below. Then, water is exposed to the heat source within a boiler, first leading to an increase in temperature of the liquid water up to about 320 ºC (red dot), at which point a few bubbles start appearing, and then producing a full conversion into steam (purple point). Hot and pressurised steam is then expanded into a turbine back to ambient pressure (light blue point), creating some mechanical power at turbine shaft. The mechanical power recovered from expanding hot steam through the turbine is larger than the mechanical power consumed to compress cold liquid, so that the cycle sees a net gain in power.
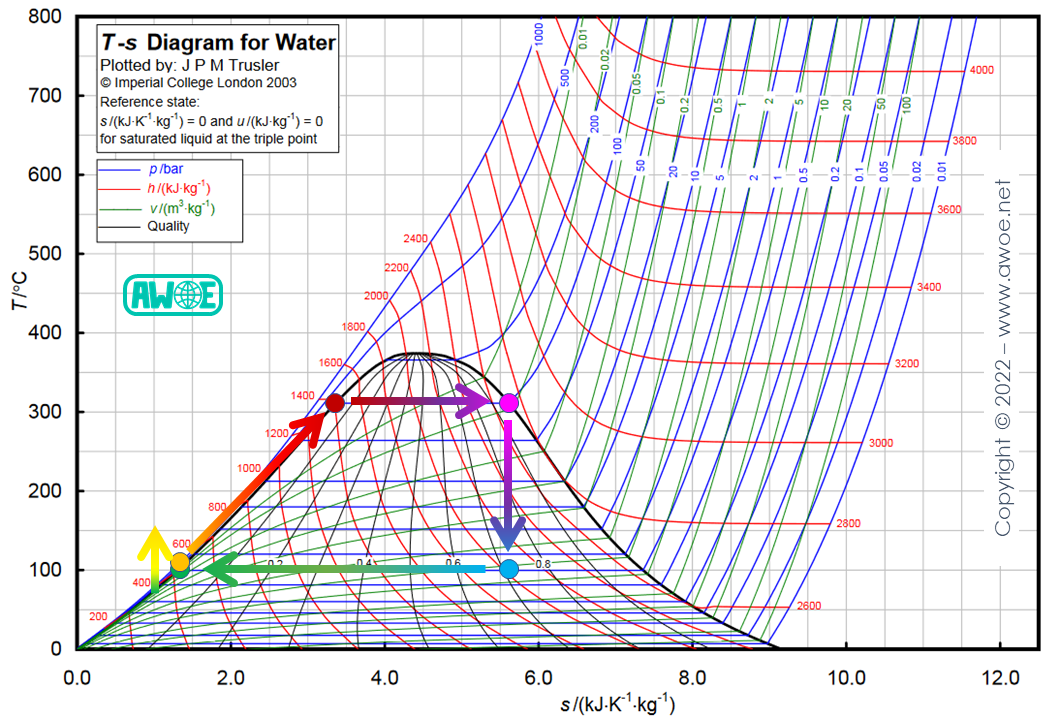
Base Rankine cycle for water/steam
A very basic setup could collect the water fraction corresponding to the blue dot (about 30% water and 70% steam) with a pump and discharge remaining steam to the atmosphere. However, this implies a large loss in working fluid, while pure water is expensive to replace. Note that the cycle only runs on pure water and not tap water to avoid mineral deposits within the circuit.
An improved setup includes a condenser that exchanges heat between the working fluid and an external cooling fluid (most likely a second water circuit at ambient temperature). The extracted heat does not reduce the working fluid temperature as long as it is kept at ambient pressure but instead absorbs heat to help transition all steam back into water.
System sizing needs to consider both the pressure capabilities of the turbine and heat exchanger with heat source as well as the heating capacity of this same source. In the example above, it is assumed that the heat source can heat up water/steam up to 320 ºC. Accordingly, the heat exchanger and the high-pressure side of the turbine need to be able to withstand at least 100 bar to prevent system bursting.
If the system can only survive an internal pressure of 50 bar, then heat exchanges need to be curtailed to keep water/steam pressure below 270 ºC or a superheater needs to be added (see below).
Exploiting the full potential of the condenser
Expanding steam down to ambient pressure means a liquid at 100 ºC at condenser outlet. However, the condenser using ambient temperature water could convert steam back to liquid at a significantly lower temperature, which also corresponds to a lower steam pressure.
If a lower steam pressure can be converted back into water to close the cycle, then the expansion within the turbine can be extended to recover more mechanical work. Considering a cooling down to about 30 ºC, expansion can be extended down to about 0.05 bar, therefore multiplying the expansion ratio by a factor of 20! This also means that the temperature ratio between the hot source and the cold source has been expanded from 593/373 (~1.6) up to 593/298 (~2.0), leading to an increase of the theoretical efficiency from 37.1% up to 49.7%.
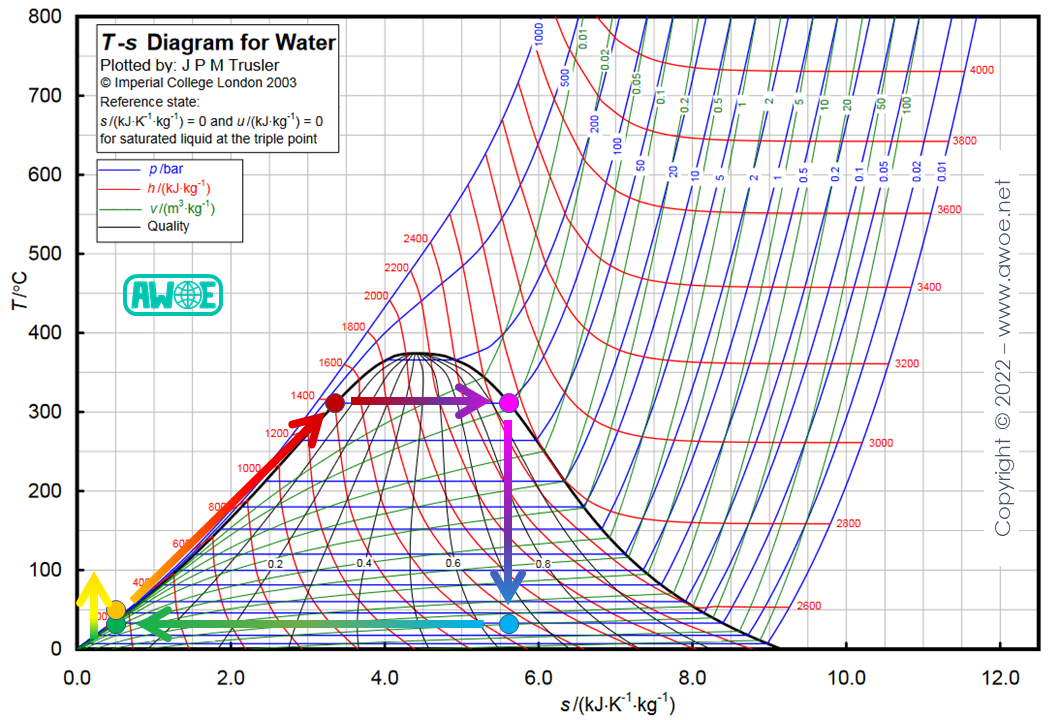
Extension of Rankine cycle expansion with condenser
Pressure ratio and vapour quality
Increasing pre-turbine pressure and decreasing post-turbine pressure both lead to an increase in water content within steam at the end of expansion. This is generally referred to as a decrease in steam quality.
As an example, with steam heated up to 100 bar and 320 ºC, expansion down to atmospheric pressure produces a mixture of 70% steam and 30% water, while expansion down to 0.05 bar produces a mixture of 65% steam and 35% water.
The problem with such large fractions of water is that water droplets in the turbine erode the turbine blades, which in turn decreases turbine efficiency. Steam quality needs to be maintained above 90% (less than 10% water) to limit erosion. Accordingly, some cycle modifications are required to keep steam quality high. Reducing system maximum pressure or increasing condenser pressure would reach that goal but at the expense of a large reduction in efficiency, which is not acceptable. Alternatively, splitting the expansion and/or increasing the heat source temperature can solve this issue.
Reheating
If the heat source temperature is below the critical temperature and steam temperature at boiler exit is the highest compatible with the heat source, the only way to improve steam quality is to split the expansion:
- high pressure – high temperature steam is expanded to an intermediate pressure (grey dot)
- the water/steam mix is reheated from intermediate temperature up to high temperature by the heat source at intermediate pressure (black dot)
- intermediate pressure – high temperature steam is expanded to the condenser pressure (blue dot)
Because of the intermediate reheating, the blue dot has now moved towards a higher steam content. Note that because the expansion ratio through the turbine in the previous low condenser pressure configuration was already as high as 2000, actual expansion in the turbine was already using multiple stages with intermediate pressure levels. Reheating is therefore just adding a heat exchange process between pre-existing turbine stages and actual reheating can include multiple reheating stages to maximise steam quality.
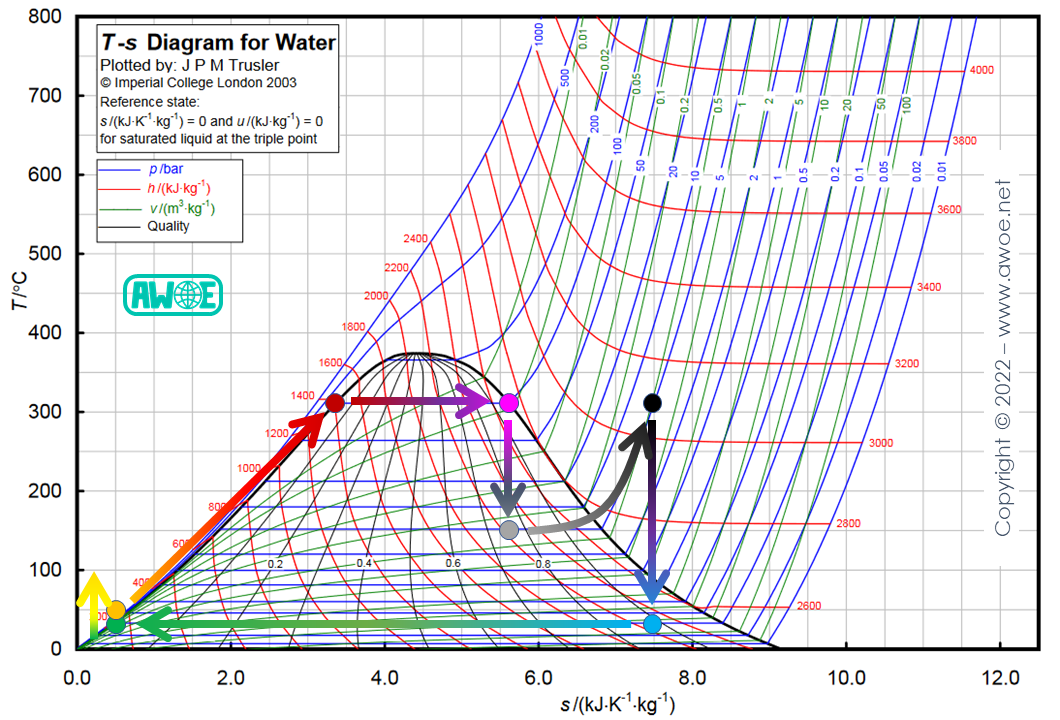
Reheating on a Rankine cycle for water/steam
Superheating
An alternative to reheating that also improves steam quality at turbine outlet is superheating. The boiler (a two-phase heat exchanger heating liquid and then vapourising it) is operated at lower pressure than the pressure corresponding to the heat source temperature. Then, the steam is sent to a superheater (a single-phase heat exchanger working on gas only) and heated up to the heat source temperature (higher entropy than at boiler outlet for the same temperature). Therefore, most of expansion within the turbine is purely in the gaseous phase and steam quality by the end of expansion is higher.
A second benefit of this approach is the operation at lower pressure which helps with piping resistance to pressure. However, the lower pressure has a negative impact on the power recovered in the turbine, so that efficiency can be reduced.
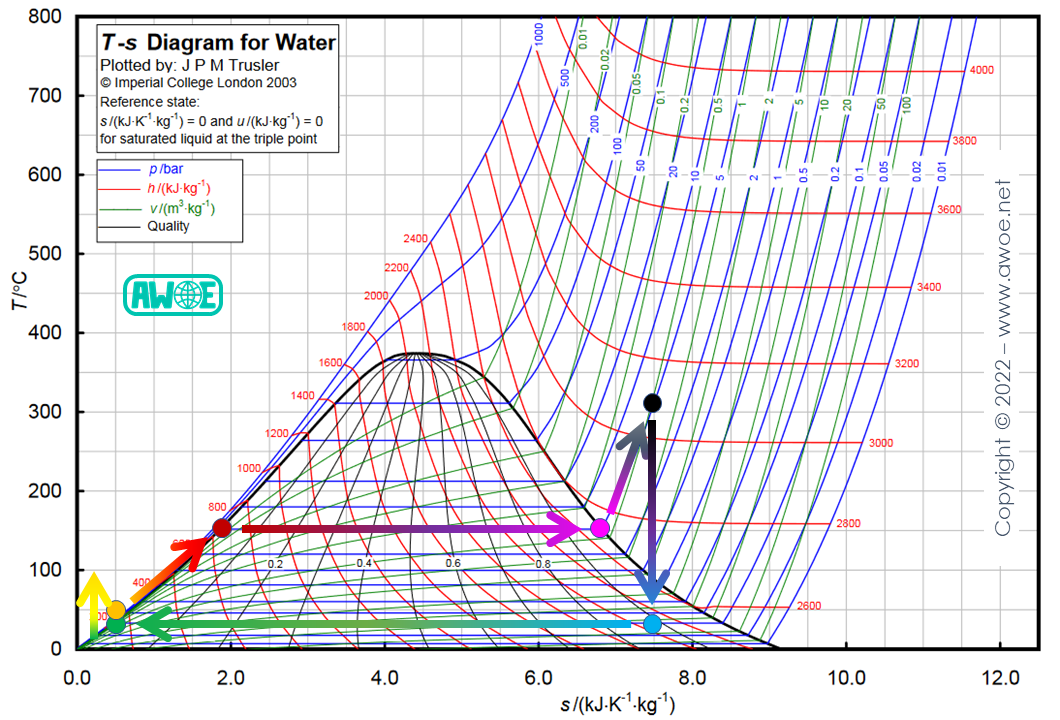
Superheating on a Rankine cycle for water/steam
Reheating and superheating
In practice, there is no reason to consider reheating and superheating as 2 competing techniques and they are often combined to maximise steam quality and keep efficiency high.
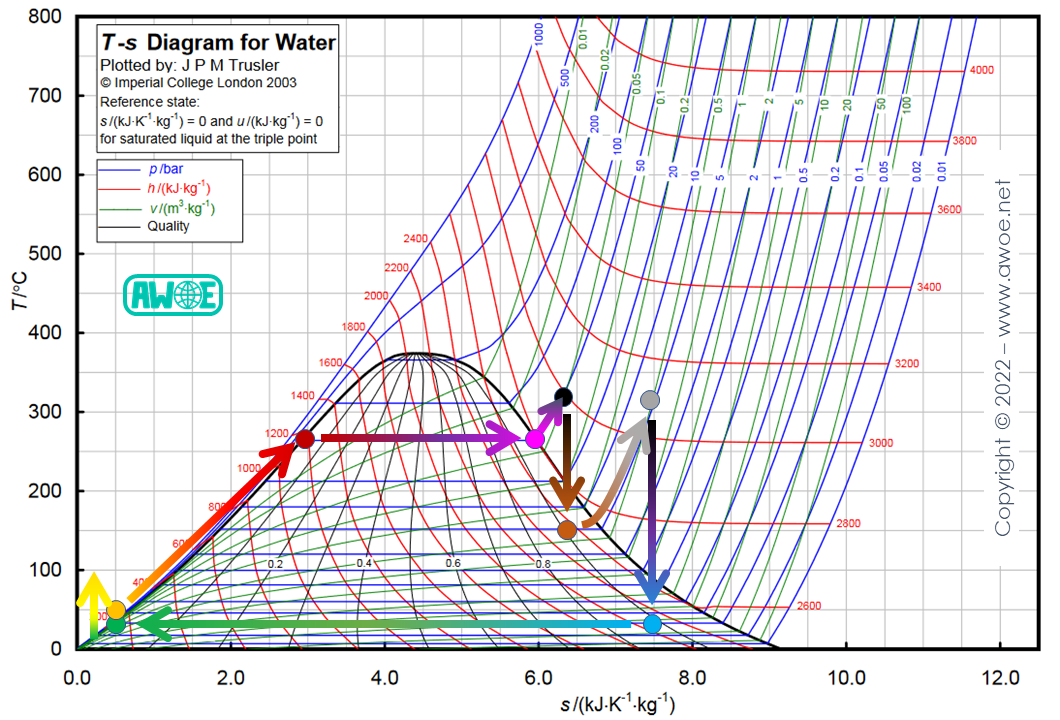
Superheating and reheating on a Rankine cycle for water/steam
Supercritical cycle
Up to now, all cycle variants were built with the same maximum temperature of 320 ºC, which is a relatively low heat source temperature. This can lead to maximum system pressure up to 100 bar. The demands on materials for piping, heat exchanger and turbine are therefore important as high temperature and high pressure are simultaneously reached and maintained for long periods of time, but modern metallurgy allows exceeding the critical pressure of water (221 bar) and reaching turbine inlet temperature up to 600 ºC.
With a heat source above 374 ºC, it is possible to operate within a supercritical cycle, never crossing the 2-phase domain from boiler outlet to the last stage of turbine expansion. This improves efficiency and ensures a high steam quality during all expansion stages.
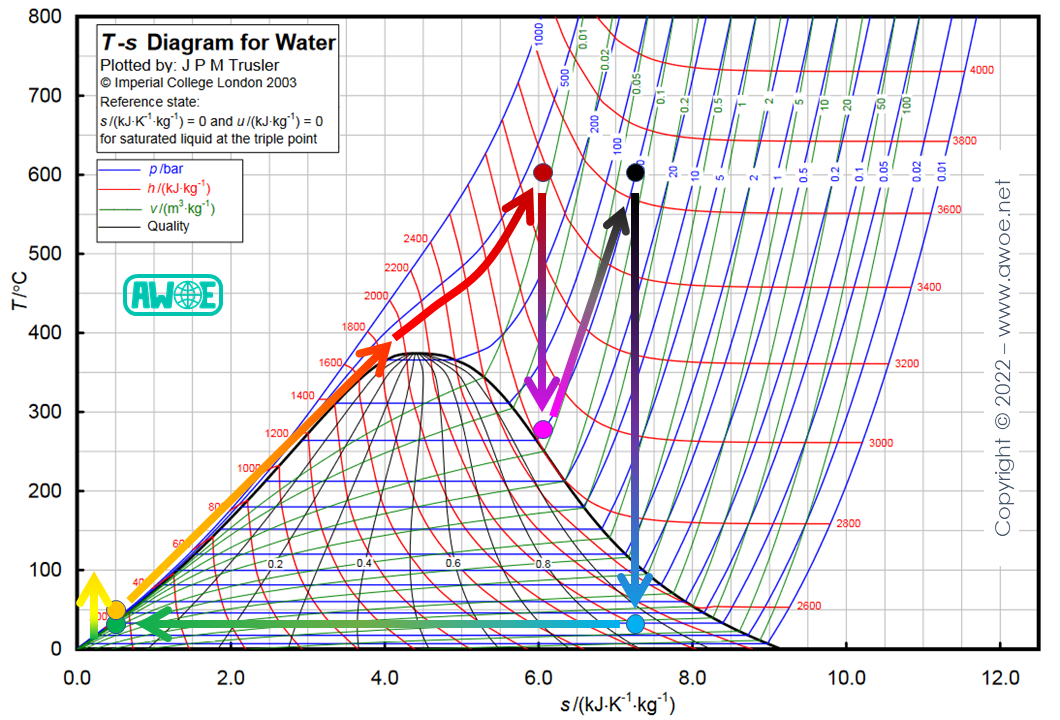
Supercritical Rankine cycle with reheating for water/steam