Syngas-to-Methanol Reactor
Published on 29 December 2021
A syngas-to-methanol reactor is a packed bed reactor fed with syngas that is internally converted into methanol with the help of a catalyst (the packed bed material).
The behaviour within the reactor is key to understand the sizing and operation of a complete methanol plant. It both defines the required pre-conditioning of syngas as well as the necessity to recycle the gaseous products and distillate the liquid products.
Chemical reactions
The reactor converts CO, CO2 and H2 into methanol (CH3OH) and water (H2O) with the help of a catalyst (generally Cu-ZnO-Al2O3) through a pair of dominating reactions:
CO2 + 3 H2 ⇋ CH3OH + H2O (Reaction 1)
CO2 + H2 ⇋ CO + H2O (Reaction 2)
Both reactions being reversible, the second allows the indirect conversion of CO through CO2. There exists a direct CO conversion path, but this appears to only have a minor contribution to the overall reaction rate [Sahibzada, 1998].
CO + 2 H2 ⇋ CH3OH (Reaction 3)
The ability to convert various streams predominantly made of either CO and H2 or CO2 and H2 means that the same reactor can cope with syngas from coal, natural gas, biomass or captured CO2 mixed with electrolysis H2.
Influence of pressure
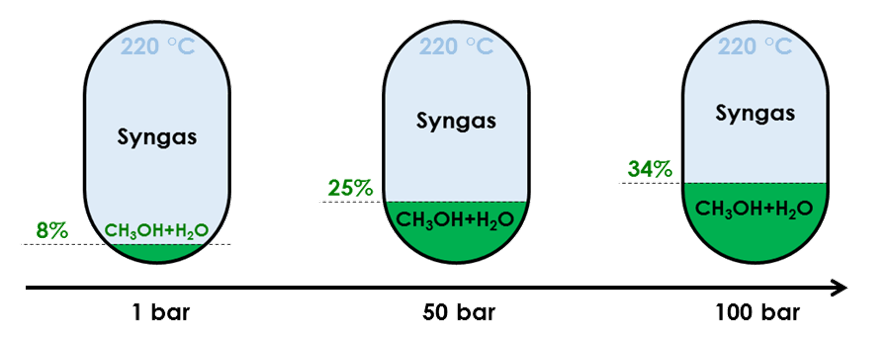
Influence of pressure on conversion rate of a feed made of 4% mol CO, 3% mol CO2, 82% mol H2 and 11%mol Ar
Since (Reaction 1) reduces the mole count while producing methanol, it is favoured by elevated pressure. A higher pressure therefore increases both the methanol yield and the amount of released heat. A higher pressure also indirectly influences reactivity by accelerating the reversal of (Reaction 2) therefore
- Producing more reactant for (Reaction 1)
- Reducing the H2O content, hence favouring (Reaction 1) equilibrium towards more methanol
Consequently, even if compressing syngas consumes energy, it is a necessity to reach a high yield. Compression has the added benefit to heat up the syngas, which is required for the reaction to occur (see below).
Influence of temperature
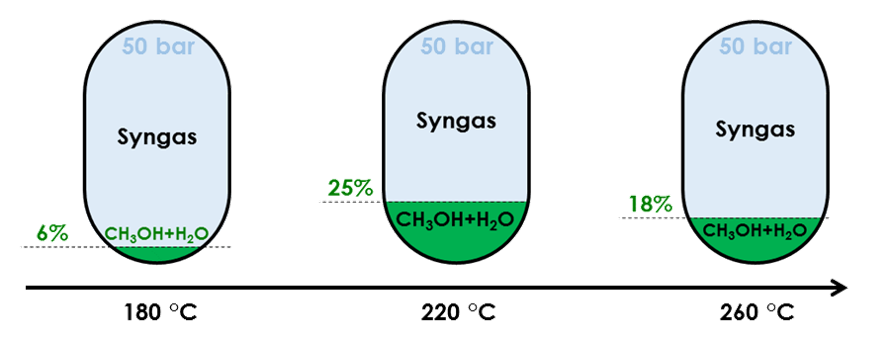
Influence of temperature on conversion rate of a feed made of 4% mol CO, 3% mol CO2, 82% mol H2 and 11%mol Ar
Temperature influences methanol yield through reactivity and equilibrium shift.
Because (Reaction 1) is exothermic, increasing reactor temperature shifts equilibrium away from methanol. Conversely, (Reaction 2) is endothermic, so that a higher temperature favours CO production. From an equilibrium perspective, the lower the temperature, the higher the yield.
Yet, temperatures below 200 °C largely reduce reactivity, meaning that slow flowing and/or huge reactors would be required, which is impractical.
In practice, most industrial applications operate between 220 and 280 °C. As temperature rises due to the overall exothermic reaction, some applications split the reactor into subsections with intermediate cooling to keep the reactant with an ideal temperature range tailored to the feed composition and pressure.
Beyond methanol yield, exceeding 280 °C has additional drawbacks: formation of by-products like methane or alternative oxygenates becomes possible, while catalyst sintering can occur reducing the reaction surface area [Mignard, 2008].
Recycling and conversion rate
Figures above highlight that whatever the selection of operating pressure and temperature, conversion rate never significantly exceeds 1/3 for a single pass through the reactor. Accordingly, high conversion rates can only be obtained by recycling the unconverted syngas back to the reactor entry.
Additionally, produced methanol and water must be separated from unconverted syngas before recycling. As all species are gaseous at reactor outlet, separation first requires cooling of reactor products to obtain a liquid methanol/water mixture on the one hand and a gaseous syngas flow on the other hand. Recycled syngas is therefore cold when mixed with hot compressed syngas coming from the source, imposing some reheating to reach favourable reactor conditions.
Heat release
Syngas conversion into methanol is overall exothermic, i.e. it releases some heat, and heat extraction favours conversion rate. Such heat can be used in multiple side process of the methanol plant, avoiding the consumption of other resources:
- Reheating the recycled syngas before mixture with the fresh flow
- Distilling the methanol/water mixture to extract pure methanol
References
[Mignard, 2008] Mignard and Pritchard, On the use of electrolytic hydrogen from variable renewable energies for the enhanced conversion of biomass to fuels, Chemical Engineering Research and Design, 86 (2008), 473-487
[Sahibzada, 1998] Sahibzada, Metcalfe, and Chadwick, Methanol synthesis from CO/CO2/H2 over Cu/ZnO/Al2O3 at differential and finite conversion, Journal of Catalysis, 174 (1998), 111-118