Life Cycle Analysis of hydrogen storage tanks
Published on 7 February 2022
Because hydrogen storage tanks widely differ in design, their production also has significantly different environmental impacts. Yet, the use of advanced materials in each case lead to a larger environmental burden than a conventional liquid fuel tank.
There are 3 types of hydrogen storage tanks for which enough data have been published to quantify their manufacturing impact (see other types):
- Type III tanks for compressed hydrogen storage, made of an aluminium liner and a composite wrapping
- Type IV tanks for compressed hydrogen storage, made of a polymer liner and a composite wrapping
- Metal hydride tanks for solid hydrogen storage, made of a steel container filled with metal powder
While Type III and IV tanks store hydrogen at high pressure (350 or 700 bar), metal hydride tanks store hydrogen at intermediate pressure (~70 bar). Consequently, during operation, the use of metal hydride tanks restricts the amount of energy spent for hydrogen compression (see Life Cycle Analysis of hydrogen compression).
Type III and IV tanks are lighter units than metal hydride tanks, so that they are the preferred choices for most mobile applications. On the other hand, the lower operating pressure of metal hydride tanks and their far lower risk of leakage makes them the best option when safety issues are the predominant concern.
Type III tanks
Type III tanks combine aluminium with carbon composite to obtain a tank that is both impervious to hydrogen and resistant to high pressure. Aluminium is in direct contact with hydrogen while a composite of carbon fibres and epoxy resin provides the additional mechanical strength.
The largest impact of the aluminium part of the tank comes from the extraction of the raw material, while the production of the carbon composite from raw materials is the main emission source from the outer layer. The environmental cost of the outer layer is dependent on where it is produced as each country (or even each region) has a different carbon intensity for power. Accordingly, a very wide range of carbon intensity values (from 6 to 70 kgCO2,eq per kg of wrapping material) have been reported for the outer layer.
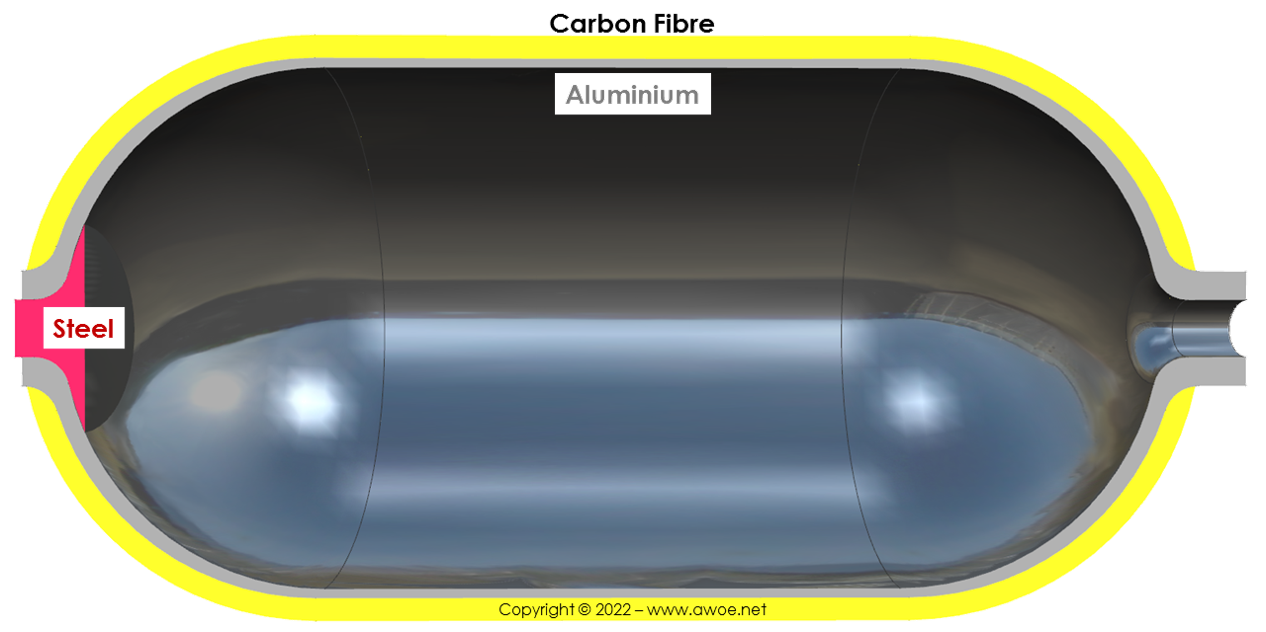
Schematic of Type III hydrogen tank
A survey of commercially available Type III tanks shows 2 main operating pressures: 350 and 700 bar. For a tank capable of storing 5 kg of hydrogen at 350 bar, the tank volume is 213.5 and the tank weight (excluding hydrogen) is 91.6 kg. For a tank capable of storing 5 kg of hydrogen at 700 bar, the tank volume is 125.9 L and the tank weight (excluding hydrogen) is 150.8 kg. Assuming a carbon intensity of 14.6 kgCO2,eq/kg for carbon fibre production, the specific equivalent emissions for each tank are 200 kgCO2,eq/kg of H2 storage capacity and 329 kgCO2,eq/kg of H2 storage capacity, respectively.
Type III tanks have a life cycle of 10 years with a mid-term inspection for safety reasons. Depending on how frequent the filling and emptying events are, their production emissions can be spread over a large quantity of hydrogen.
Type IV tanks
Type IV tanks have a similar structure to Type III tanks but replacing aluminium by a high-density polymer as liner material. The objective is a reduction in tank weight.
The carbon composite wrapping remaining the main material, the same large variation in equivalent greenhouse gas emissions results from the location of composite manufacturing. Furthermore, some manufacturers choose a relatively thin polymer layer and add a fiberglass layer around the carbon composite to improve mechanical properties. Yet, fibreglass can also be a material with a large environmental impact during production.
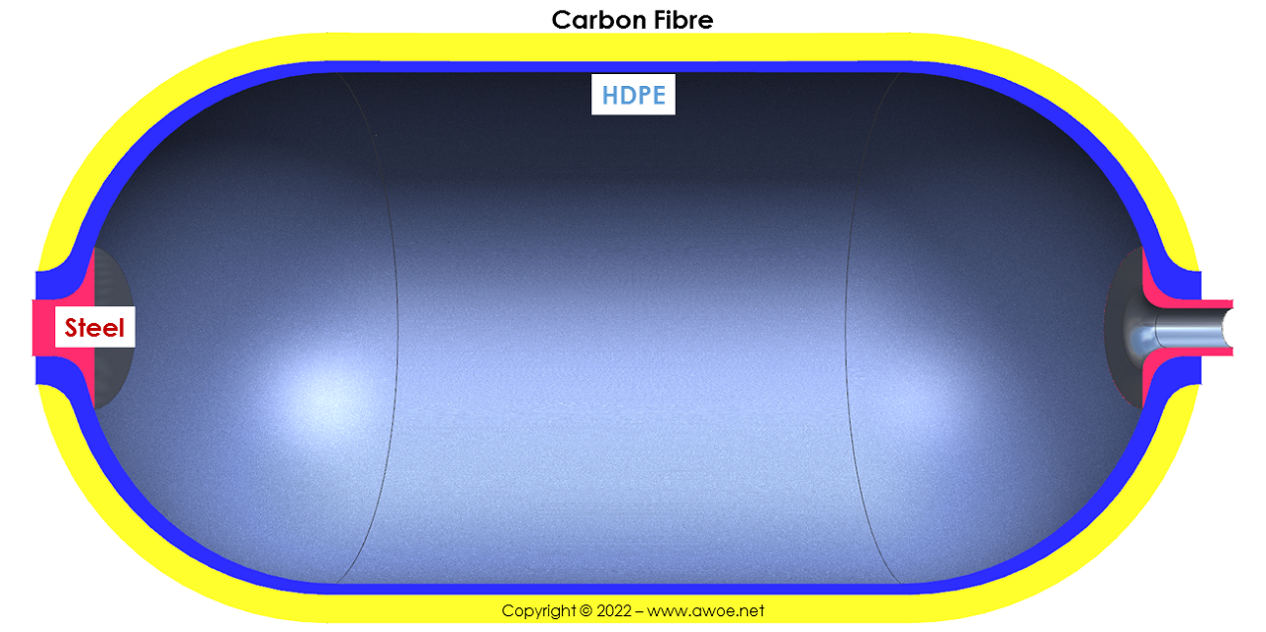
Schematic of Type IV hydrogen tank
A survey of commercially available Type IV tanks shows a significant weight gain compared to Type III tanks. For a tank capable of storing 5 kg of hydrogen at 700 bar, the tank volume is still 125.9 L, but the tank weight (excluding hydrogen) is reduced down to 96 kg. Assuming a carbon intensity of 14.6 kgCO2,eq/kg for carbon fibre production, the specific equivalent emissions are 221 kgCO2,eq/kg of H2 storage capacity. Accordingly, both the weight and the carbon intensity of a Type IV hydrogen tank operating at 700 bar are very similar to those of a Type III tank operating at 350 bar. The key difference is the reduction of storage volume by 40%, which is key within light duty vehicles. Yet, because of the extra energy (and environmental) cost of compressing hydrogen from 350 up to 700 bar, the Type III tank might be a better choice for applications being less constrained by packaging.
Similarly to Type III tanks, Type IV tanks have a life cycle of 10 years, so that production emissions can be distributed over many fuelling events, largely restricting the tank contribution to each event.
Metal hydride tanks
Rather than storing hydrogen as a compressed gas, metal hydride tanks rely on hydrogen absorption within a metal powder. Accordingly, such tanks do not require such a high operating pressure (operation below 100 bar).
However, the amount of hydrogen that can be stored within the metal power is restricted to a few percent in mass, so that a large mass of metal hydride is required. In addition, the metal powder must be stored in a tank that can withstand both the pressure level and the weight of powder, leading to a widespread use of steel.
A tank storing 5 kg of hydrogen would therefore weigh about 716 kg, 222 kg being metal hydride(s) and 278 kg being the steel casing, within a volume of about 141 L. Metal hydrides being complex materials requiring energy intensive production methods, their carbon footprint is large. Combined with a large mass of steel, such a tank has specific equivalent emissions of about 2057 kgCO2,eq/kg of H2 storage capacity, i.e. 9 times those of a Type IV tank.
While not appropriate for cars because of weight, the safety benefits of moderate pressure and total absence of leaks make it suitable for stationary applications even in populated areas. But because the technology is relatively new, there is no clear conclusion on their life expectancy, so that it is impossible to say if comparing 2057 kgCO2,eq/kg of H2 storage capacity with 221 kgCO2 is a fair comparison.
Comparison with a fuel tank for liquid hydrocarbons
Numbers above have been obtained by sizing a tank for 5 kg of hydrogen storage. A fair comparison with a conventional petrol fuel tank requires to size a liquid fuel tank for the same vehicle range.
A MY2020 Toyota Mirai has a tank capacity of 122 L (~5kg) and a rated range of 502 km (i.e. drives 103.6 km per kg H2), while a MY2021 Toyota Mirai has a larger tank and an improved specific range of 115.5 km per kg H2 (range of 647 km). The latest Toyota Mirai (MY2021) would therefore travel 577.6 km with 5 kg of hydrogen available in the tank.
The average fuel consumption of new cars in Europe is about 120 gCO2/km, i.e. 5.17 L of gasoline per 100 km. A range of 577.6 km with gasoline therefore requires a tank of 29.9 L.
A steel fuel tank of about 30 L for gasoline would weight about 5.5 kg, 88% being steel, the rest being paint/coating. However, tank manufacturing will scrap an additional 1.5 kg of mild steel sheet during forming and cutting, so that the relevant raw steel mass is about 6.5 kg. Once accounting for raw material emissions and manufacturing operations, the sourcing of such a tank emits 17.4 kgCO2,eq, i.e. the equivalent of about 3.5 kgCO2,eq/kg of H2 storage capacity.
A plastic fuel tank of about 30 L for gasoline would weight about 5.3 kg, 90% being high-density polyethylene, the rest being resin and ethylvynil alcohol. Forming HDPE does not involve significant waste but consumes more electricity. Once accounting for raw material emissions and manufacturing operations, the sourcing of such a tank emits 9.1 kgCO2,eq, i.e. the equivalent of about 1.8 kgCO2,eq/kg of H2 storage capacity.
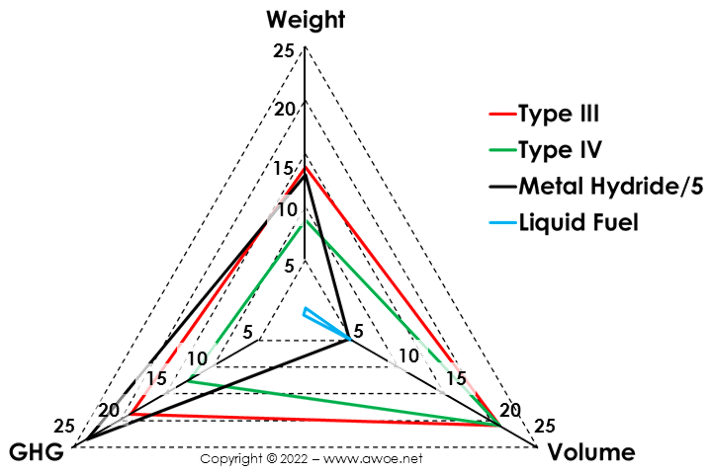
Comparison of various hydrogen storage technologies with a liquid fuel tank for hydrocarbons
Accordingly, whatever the selected type of fuel tank, the storage tank for liquid hydrocarbon fuels has a negligible environmental impact compared any technology to store hydrogen. In addition, the storage tank for liquid hydrocarbon fuels is a lot smaller, a lot lighter and can be more freely shaped to accommodate packaging within the vehicle.