Water Consumption in Concentrated Solar Powerplants
Published on 18 November 2022
A Concentrated Solar Powerplant collects sun energy as heat which is then converted into torque by a steam turbine running a Rankine cycle. Maximising efficiency on a Rankine cycle requires good cooling to condense the steam exiting the turbine. Best cooling is obtained with cooling towers spraying water to use its evaporation to absorb heat.
Another significant source of water consumption is the cleaning of mirrors. This is regularly performed (always at night to avoid interrupting production and creating thermomechanical stress) to ensure that the optical performance of mirrors is always optimum. Other sources of water consumption are minor, like maintaining water content in the steam cycle, water losses in the water treatment process, or human consumption of water in the plant.
The cooling towers consume about 94% of total water consumption, while mirror cleaning represents about 4% of water consumption. In an arid environment, such 94% of water consumption should be avoided because water resources are scarce and mirror cleaning cannot be skipped.
Eliminating the water-based wet cooling in towers is possible with dry cooling, which only uses an air flow to condense steam. However, dry cooling cannot reach as low temperatures as wet cooling, so that the efficiency of the Rankine cycle is a bit degraded.
Bulb air temperatures
Measuring air temperature can deliver different results depending on the way the thermometer is used:
- A thermometer freely exposed to air but shielded from any radiation and moisture will read what is called the dry-bulb temperature, which is the true thermodynamic temperature
- A thermometer wrapped in a soaked cloth will read what is called the wet-bulb temperature; it corresponds to the temperature of air cooled to saturation (100% humidity) by the evaporation of water contained in the air
Because of the significant latent heat of vapourisation of water, the wet-bulb temperature is lower than the dry-bulb temperature. As a matter of fact, it is the lowest reachable temperature based on water evaporation only.
In an arid environment, the humidity content of air is very low and there is a significant difference between the dry-bulb and the wet-bulb temperatures (about 16°C for a dry-bulb temperature of 36°C). Accordingly, there will be a significant gap in cooling efficiency between a dry cooling system (cooling at best to dry-bulb temperature) and a wet cooling system (cooling down to wet-bulb temperature thanks to air saturation with water sprays).
Dry cooling
Dry cooling only uses a draft of air over a heat exchanger or a set of finned tubes promoting heat transfers between the steam to be condensed and the cooling air. To increase the cooling capacity with respect to natural draft, fans are often added to increase air flow rate as well as the coefficient of convection around the exchanger tubes.
The fans can be installed upstream or downstream the heat exchanger, pushing the air through (forced draft) or pulling the air through (induced draft) the heat exchanger. Pulling is generally preferred because fan energy consumption is lower and the good control of exhausted air flow prevents immediate recirculation of the extracted hot air.
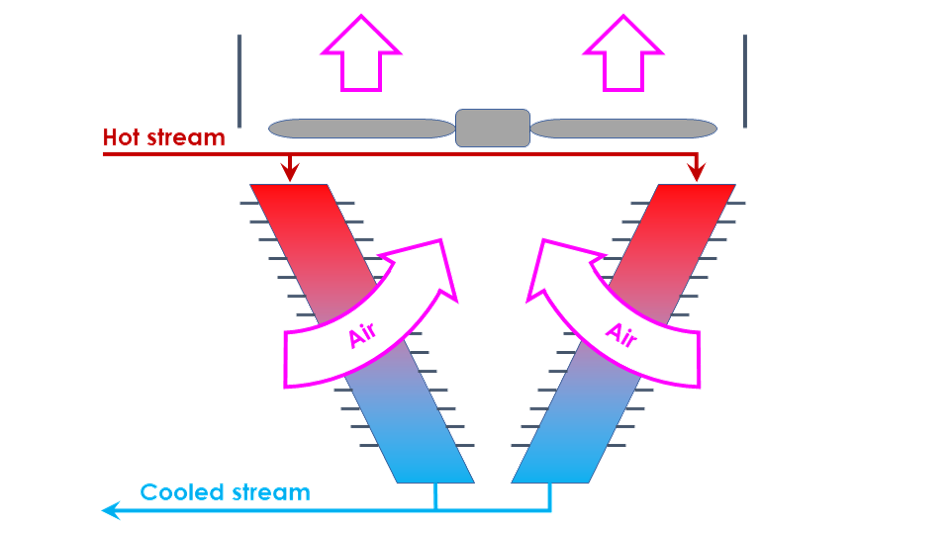
Schematics of a dry cooling set-up
Wet cooling
In addition to air draft, wet cooling ensures air saturation by spraying some water upstream the heat exchanger, so that the reference temperature for heat exchanges shifts from dry-bulb to cooler wet-bulb temperature. To ensure saturation, spraying generally flows more water than required to saturate air and excess water is collected and sent back to the spraying circuit.
However, each evaporation cycle will consume pure water and leave the impurities within the unevaporated water, so that the recirculated water has a rising concentration in dissolved salts. Accordingly, water needs replacement after a few cycles to avoid building up scale on the heat exchanger. To avoid stopping the installation to swap the cooling water, a continuous replacement process is used with a blowdown of a fraction of the recirculated water and an addition of an equal amount of fresh clean/treated water. This process adds to water consumption beyond water evaporation itself.
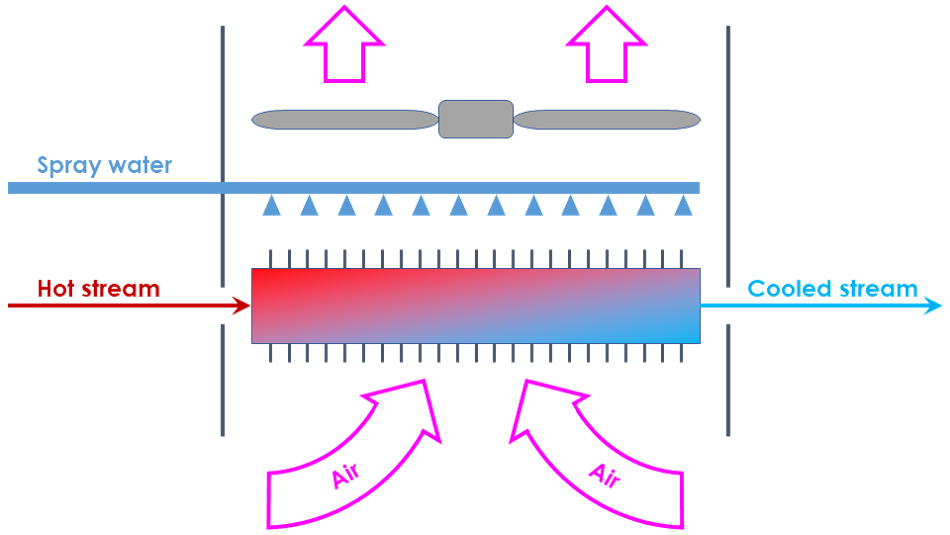
Schematics of a wet cooling set-up
The wet condensing system includes a steam surface condenser, circulating water pumps, an induced draft counter-flow cooling tower, as well as an underground and aboveground interconnecting pipe network. Despite this complex set-up, the large requirement for fans in a dry-cooling system with identical cooling capacity means that the dry cooling system will be about 30% more expensive.
Water consumption savings vs Efficiency loss and Increased electricity cost
Because dry cooling does not reach as low temperatures as wet cooling, it degrades the efficiency of the Rankine cycle (a higher cold temperature in the Rankine cycle equates to a higher minimum pressure while peak pressure is kept unchanged, reducing the overall power output). On a hot summer afternoon, if the steam cycle efficiency of a wet-cooled system is 37.7%, the corresponding efficiency with an aggressive dry-cooled system would be around 35.8%.
A lower Rankine cycle efficiency for a given solar field means a lower overall power generation and therefore a higher electricity cost as the initial investment (mainly the unchanged solar field and power block) is amortised over a lower production. NREL estimates that dry cooling in arid environments leads to up to 8% increase in electricity cost, but with the benefits of saving more than 90% of water consumption.
A wet cooling system can bring water within 5°C of the wet-bulb temperature. Such water can then condense steam to a temperature only a few degrees higher than its own temperature. Accordingly, the difference between wet-bulb temperature and steam condensate can be kept around 10°C.
A dry cooling system can only condensate steam at a temperature above the dry-bulb temperature. Because air has a low volumetric heat capacity, it requires large volumetric flow rates to produce cooling and can only condense steam to temperature more than 15°C above dry-bulb temperature. In addition, the large volumetric flow rates necessitate large fans which consume some energy.
In an arid climate, a dry-bulb temperature of 36°C will correspond to a wet-bulb temperature of about 20°C. A dry cooling system could at best condense steam down to 51°C. Under identical ambient conditions, a wet cooling system could reach a steam condensing temperature of 30°C.
Note that because condenser pressure and temperature are linked within the Rankine cycle, a high condensing temperature will also produce a higher turbine backpressure. Therefore, appropriately designed power blocks for dry and wet cooling would use different turbine designs.
Because dry cooling leads to a reduction in Rankine cycle efficiency, the overall CSP efficiency is reduced. There are 2 options to recover power output:
- Enlarging the solar field to increase the heat input
- Oversizing the dry cooling system to reduce the gap between dry-bulb temperature and condensation temperature
From an economic perspective, oversizing the dry cooling system although not cheap is still a lot cheaper than enlarging the solar field. While oversizing the dry cooling system cannot reach the performance of wet cooling, it can effectively minimise the degree of solar field enlargement and produce the best economic trade-off.
The dry cooling energy consumption and the oversizing of the cooling system leads to an increase in auxiliary energy consumption by 15-20%. On the other hand, the water consumption for a 100 MW CSP units would reduce from ~3.5 m3/h with wet cooling down to ~0.3 m3/h with dry cooling (mainly mirror cleaning). For reference, a nuclear powerplant of 100 MW would have a water consumption of ~3.2 m3/h using wet cooling.
A side benefit of wet cooling systems is the more consistent condensing temperature over the operating temperature range, leading to a more consistent turbine exhaust pressure. This more consistent exhaust pressure maintains operation closer to the peak efficiency point of the power block.
Hybrid cooling
Dry cooling saves a lot of water and is only really detrimental under very hot ambient conditions, i.e. conditions that are only encountered during a part of daytime on a limited number of days during the hottest season (hot summer afternoons). A hybrid cooling system including both a dry cooling and a wet cooling section is an effective way to reach a positive trade-off between efficiency and water savings.
Under most conditions, only dry cooling would be in operation. Under the extremely hot conditions leading to large gains with wet cooling, such a wet cooling would increase efficiency, while overall water consumption is kept low by limiting the duration of such wet cooling events. While effective for efficiency and water consumption optimisation, such a method might not lead to electricity price gains as the initial investment will have to include both a dry and a wet cooling system. A further economic optimisation may then include a limitation in sizing of the individual cooling systems, so that full cooling capability would only be reached by using simultaneously the full (or at least most of the) capabilities of both dry and wet cooling.
An alternative cheaper approach in terms of initial investment would be to only build a dry cooling system with added sprayers in the incoming air flow. Such sprayers would only be activated during the hot summer afternoons and will not deliver as much water as a wet cooling system since the goal would be to add moisture in the air without reaching full saturation as this would require collecting excess spraying. The air cooling system would then operate at a temperature somewhere between dry-bulb and wet-bulb temperature, improving cooling for a moderate water consumption and a marginal added investment.
Benefit of heat storage
Dry cooling is only really an issue if power is generated under the most intense solar irradiation. When operating a CSP with large heat storage capacity, most solar energy is collected under the most intense solar irradiation, but most power is produced off these conditions, partly at night when ambient conditions are a lot cooler. Large heat storage to reach continuous daily production therefore reduces the gap between dry and wet coolng.
When heat storage in a CSP is combined with some solar panel on the same site, then electricity is only produced during daytime by the solar panels and all heat collected by the CSP is converted overnight. The hot conditions that are unfavourable to dry cooling therefore never happen during power generation with the Rankine cycle.