Life Cycle Analysis for Wind turbines
Published on 29 December 2021
Wind turbines are a source of renewable electricity without any contamination or emissions during operation, except for the maintenance operations. Yet, their true environmental impact results from emissions during manufacturing (raw material extraction + conversion into parts), installation, maintenance and disposal.
Most emissions are linked to manufacturing or installation and are upfront emissions, meaning that almost all emissions are released before the wind turbine produces any electricity. Accordingly, the higher the effective production of electricity once in operation, the lower the emissions per produced kWh. Selecting a favourable wind farm location is therefore simultaneously important for energy output, economic output (more power for the same investment) and environmental rating (more power for the same emissions, i.e. less emissions per produced kWh).
Environmental impact of wind turbine subassemblies
The main contributors to the environmental impact of wind turbines are the tower (mainly made of steel) and the foundation/floatation assembly (mainly made of concrete (on-shore) or steel (off-shore)). Their impact results from a combination of
- A large mass of material used for these parts
- The CO2 emissions resulting from steel and concrete production
- The weight of such materials negatively influencing transport impact
The relative impact of steel and concrete on the final balance depends on the recycling effort at the disposal stage. While sourcing required ore and manufacturing steel might have a larger impact than sourcing components and manufacturing concrete, recycling of all metal parts of a wind turbine is possible, significantly cutting the environmental cost of steel.
The wind turbine subassemblies that are practically not recycled are the blades made of a complex multi-layered composite and the concrete foundation of on-shore and near-shore installations. Blade recycling is possible but it is more expensive than producing new ones, while some studies even suggest that energy consumption for recycling is larger than for production of new units.
Life Cycle Analysis
The Life Cycle Analysis (LCA) of a wind turbine is generally performed over a period of 20 years, by which the largest components need replacement. Some equipment like the generator, the gearbox or the rotor blades might have to be replaced after 10 years. Yet, their environmental impact is so low compared to the tower and foundations that it is beneficial to replace them while reusing the most polluting elements.
The key resource that defines the environmental impact of wind turbines is steel. It is used for the structure in all applications, for the foundation in near-shore wind turbines, and for the floatation device in far-shore wind turbines. In the structure, the largest fraction of steel use relates to the tower, while it is also used in the nacelle structure as well as in the conversion unit (generator, gearbox and transformer). The large influence of steel comes from a combination of (1) emissions during ore extraction and production of raw steel and of (2) large quantities used within each turbine. It is noteworthy that steel influence on LCA results largely varies from one application to the other depending on the amount of recycling efforts at end-of-life (recycling metals in wind turbines can cut their equivalent CO2 emissions by up to 90%!).
Another important resource is concrete for on-shore applications and some near-shore applications. As for steel, the impact of concrete is a combination of emissions to produce the raw material and the large quantity used in foundations. Unlike steel, concrete is rarely recycled. Yet, by the end of a 20-year cycle, a new on-shore application is often proposed on the same site, allowing to reuse the existing foundations, replacing recycling by reconditioning, still saving resources and equivalent CO2 emissions.
Because 90+% of emissions come from manufacturing and installation of wind turbines, the emissions are upfront and the carbon intensity becomes very dependent on the amount of energy produced to compensate them. This explains why
- Even the same turbine can induce a different carbon intensity as a function of installation method and location
- A larger turbine is beneficial through increasing both the power output and the number of full load hours, so that production increases quicker than emissions
- The location is key to ensure long hours of full load operation, i.e. a high capacity factor, with a notable advantage for off-shore sites compared to on-shore sites thanks to more continuous wind conditions
- The installation method for off-shore applications has a large influence through the added emissions for the foundations or floating platform
The equivalent greenhouse gas effect of building and operating wind turbines, also known as the carbon intensity, is generally expressed in equivalent CO2 emissions. The range of specific equivalent CO2 emissions for wind turbines, either on-shore or off-shore, is 7 to 38 gCO2,eq/kWh, with numerous projects below 20 gCO2,eq/kWh. Compilation of published data clearly shows that both increased turbine size and increased capacity factor lead to lower specific emissions (both through more energy output), while distance-to-coast and platform design in far-shore applications can have a significant negative impact.
Sensitivity studies to turbine size shows that the optimum is the smallest wind turbine that adapts well to the average wind speed , i.e. the lowest upfront emissions while not impeding productivity.
There are 2 key differences between on-shore and off-shore applications
- Wind speed: on-shore wind speed is lower than off-shore wind speed, so that off-shore applications have larger, more powerful turbines
- Wind availability: on-shore capacity factor lies between a tenth and a third, while off-shore capacity factor lies between a third and a half
With larger, more powerful turbines (up to 8 MW) and longer full load operation (up to 4300h/y), the energy output per off-shore turbine can be 5 times larger than a typical on-shore application (power around 3 MW and operation for ~2000h/y). Yet, off-shore applications require more raw material and larger upfront emissions, so that they do not necessarily lead to a lower carbon intensity.
On-shore applications
The compilation of various LCA's shows that 80+% of emissions from an on-shore wind turbine come from raw materials only, mainly steel (tower, nacelle, rotor) and concrete (foundation). As highlighted by many LCA's, the tower and foundations represent about half these emissions. Their sizing is mandated by safety, mainly the most adverse wind conditions that could be met during the 20-year life of the wind farm in order to avoid any risk of tower collapse.
The traditional structure of a wind turbine tower is a tube with narrowing cross-section towards the top. The production method is complex and performed in specialised factories before shipping to the installation site. The towers are generally made of a few sections connected with pre-stressed bolts across dedicated flanges and installed with specialised cranes.
To reduce the environmental impact of the tower and foundations, some research groups are investigating alternative structures with potentially less energy or material requirements. For example, shifting to a lattice tower structure (think of a straightened single leg of the Eiffel Tower) saves both materials (less steel required) and specific equipment requirements (no special factory, no structure transport over long distance, no specialised crane). Comparing identical height structures capable of supporting the same loading, the lattice tower saves up to 35% in steel, further reducing foundations requirements by up to 33%. The tubular nature of the tower also means that transportation of large structure from faraway factories is avoided.
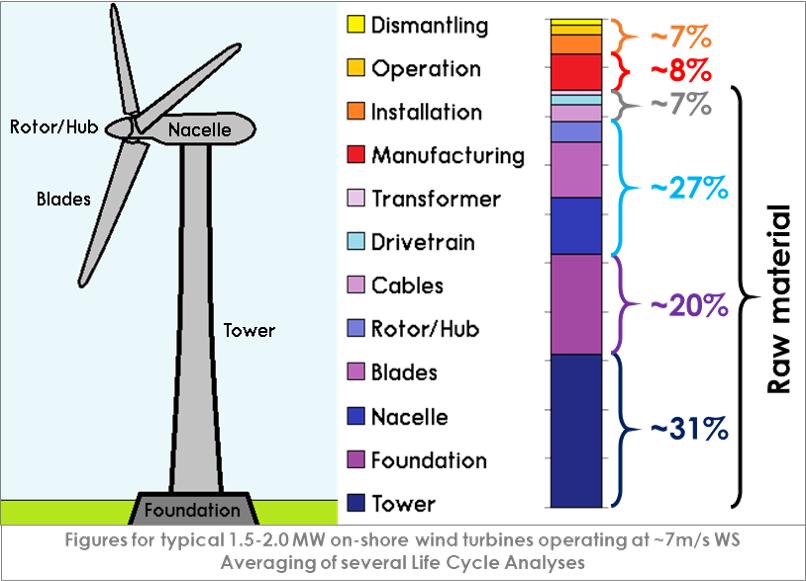
Most emissions being released before operation, the carbon intensity (CI) of a wind farm heavily depends on maximising produced energy (CI = emissions / total energy) through long operating hours (high capacity factors). Coastal areas with annual average speed over 7 m/s at 50 m height are very advantageous in this respect, as can notably be found in Northern Europe or in Brazil. A typical on-shore wind turbine located in an area with annual average speed around 7 m/s has a power output of 1.5 to 2.0 MW and a CI ranging from 7 to 21 gCO2,eq/kWh, mainly depending on wind regularity.
Note that a diligent work at wind farm planning stage is not enough if the electric grid is unable to absorb power output. If power output exceeds grid capacity on windy days, it prompts curtailment (shutting off turbines), effectively increasing turbines’ CI by cutting their effective operating hours. Having some on-demand energy storage through electricity conversion avoids energy waste and keeps actual CI low.
Off-shore applications
Off-shore applications are subdivided into two subcategories: near-shore sites are in shallow water and within 20/25 km from the coast, while far-shore sites are in deep water and further away, with projects up to 200 km off the coast.
A near-shore installation is very similar to an on-shore one with an adaptation of foundations to the marine environment and improved wind conditions. Contrarily, far-shore applications require dedicated (generally floating) concepts, different grid connection approaches as well as revised operation and maintenance strategies, imposing larger investments and creating larger emissions at wind farm creation. Yet, far-shore wind conditions are a lot more favourable with wind speed around 10 m/s and a capacity factor close to 50%, so that energy output is also significantly higher. These competing factors imply that shore distance and water depth only have a marginal effect on carbon intensity when comparing project around the limit between near-shore and far-shore .
To provide a fair comparison, any on-shore or off-shore site must be analysed including the transmission cables to connect to an on-shore grid connection point. For off-shore applications, this requires the additional consideration of the connections between turbines and the park transformer as well as the high voltage connection from the wind farm to the on-shore grid connection.
Near-shore applications
Near-shore applications have wind turbine foundation anchored to the sea bed in a similar fashion to on-shore applications but with some extension. The extension can be a tall concrete foundation, a monopile (i.e. a long steel extension to the tower with the lower end buried into the ground) or a lattice structure anchored to the sea bed. Whatever the selected solution, it implies more material used for foundations (more concrete or more steel) and more equipment and resources required for installation and disposal.
Accordingly, compared to an on-shore application, the relative importance of the tower, nacelle, and rotating assembly decreases in terms of equivalent greenhouse gas emissions. The foundations become by far the largest contribution, with all non-turbine components (installation, operation, disposal) becoming another significant item. Finally, the electrical connection side also has a growing importance, mainly due to the extended cabling required.
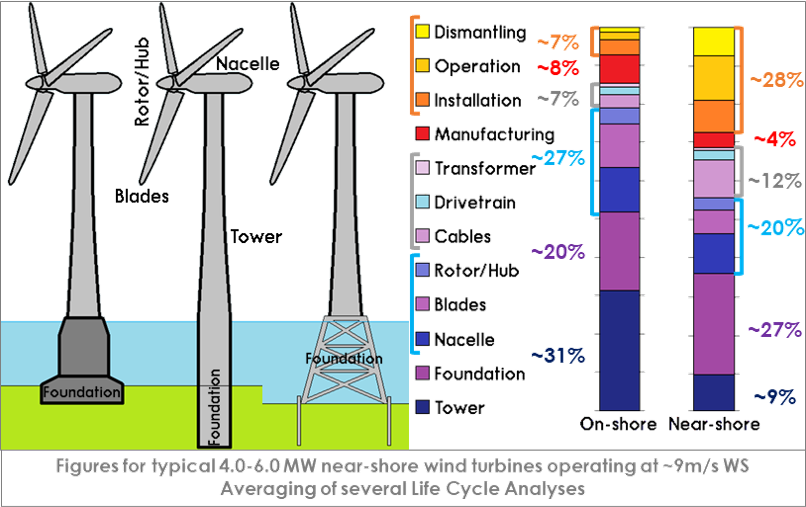
Although having larger greenhouse gas emissions, near-shore wind turbines have very similar specific equivalent CO2 emissions (8-23 gCO2,eq/kWh) to on-shore applications (7-21 gCO2,eq/kWh) because they generate more electricity. Higher oversea wind speed allows more powerful turbines and more frequent windy conditions lengthen operating hours, so that more energy is generated (energy = power x time). This, of course, only holds true when comparing wind farm implementations in the respective best conditions. Comparing on-shore wind turbine in Scotland with a near-shore wind turbine off the Balearic Islands would certainly not lead to the same conclusion.
Far-shore applications
A far-shore wind turbine operates in deep waters, so that rigid anchoring to seabed is impractical. It therefore needs to be a floating installation with some loose anchoring to avoid drifting and some cabling to harvest power output. Beyond floatation, the platform also has to insure stability for a tall tower excited at top by strong wind.
Well-established floating oil rig technology can fulfill such requirements, explaining the early implication of Oil & Gas companies and subcontractors in most projects. As of 2021, there are only 3 commercial floating wind farm projects, off the coast of either Scotland (2) or Portugal (1). The first one was Hywind Scotland commissioned in 2017 with Equinor as the largest shareholder.
Whatever the platform design, it is mainly made of steel and uses more of it than the turbine tower itself. Accordingly, the platform has the largest influence on the carbon footprint of the wind farm and the complete setup can only have a reasonable carbon intensity if electricity production is high.
All commercial floating wind farms use wind turbine of 5 MW of larger. Combined with high capacity factors, high power leads to the required energy output to compensate the environmental impact of the floating platform. Research based on 5 MW turbines estimates that the turbine itself has a carbon intensity of less than 5 gCO2,eq/kWh but the platform adds between 6 and 20 gCO2,eq/kWh. Beyond the platform, the increase in emissions from maintenance, installation and decommissioning can be as high as 7 gCO2,eq/kWh. Cables, mainly through aluminium production, are the second contributor to the platform impact with cable link to the shore contributing to about 2 gCO2,eq/kWh. The resulting range of equivalent CO2 emissions is 16 to 38 gCO2,eq/kWh, i.e. larger than for most on-shore or near-shore applications but with a far higher and more continuous power output.